228. Magneto-Elastic Sensing For Structural Health Monitoring
Team
Name | Role | Primary |
Andrei Zagrai | Principal Investigator | ● |
Nick Demidovich | Tech Monitor | ● |
Danielle Monette | Fiscal Admin | ● |
Lisa Oty | Fiscal Admin | ● |
Gayle Bailey | Contract Admin | ● |
Project Description
Structural health monitoring (SHM) is seen as a key technology to reduce cost land improve safety of operation of modern space vehicles. Future spacecraft require sensing technologies that are reliable, multi-purpose, durable, and long-lived. These sensors need to detect and characterize impact damage from space debris, assess structural integrity of the spacecraft, provide information on structural interfaces, explore spacecraft electrical signature, enable reusable component requalification for flight, and possibly conduct non-contact inspection in space.
Project Outcomes
- Develop adequate analytical and numerical models which describe magneto-elastic damage detection.
- Investigate potential of the magneto-elastic SHM for characterization of interfaces in space structures and assessment of incipient fatigue damage before crack development.
- Explore damage manifestation in the magneto-mechanical sensor signature and suggest respective feature extraction algorithms.
- Consider methodologies for features classification / damage characterization that enable integration of the above mentioned components into a comprehensive SHM system.”
Summary of Output
● Near-Term: explore if embedding sensors that can be pulsed with magnetic fields can yield reduction of space vehicle qualification time (and cost) via real time monitoring of structural interfaces during and after assembly, on-orbit diagnosis and system characterization – would enable rapid turnaround/flight rates of RLVs
● Far-Term: deploy to industry if successful
Quad Chart
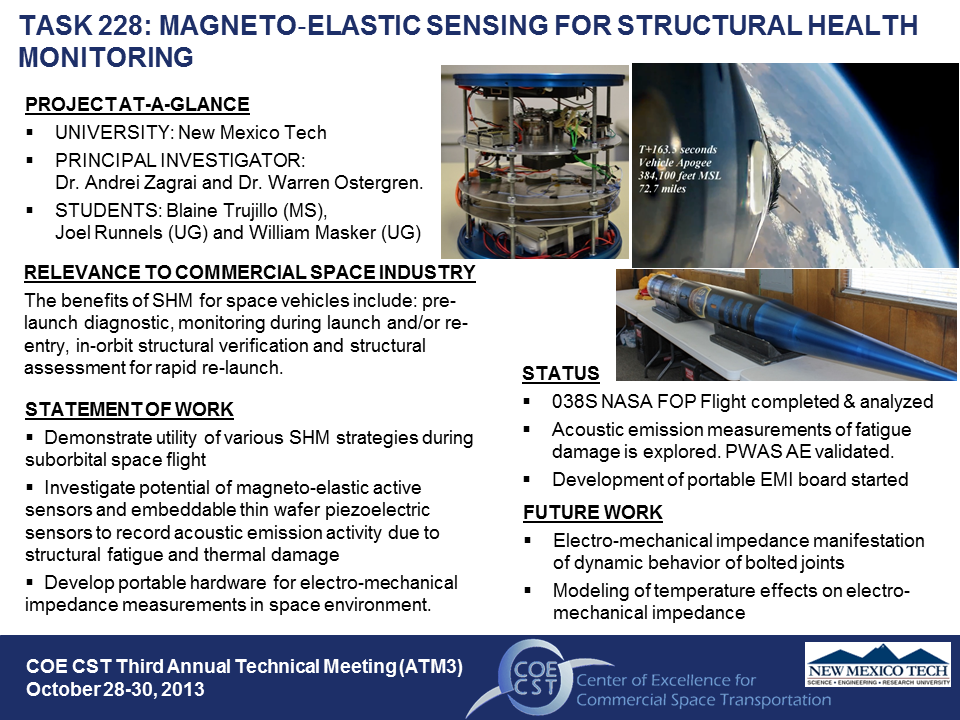